Destylacja rozpuszczalników to proces, który polega na oddzieleniu substancji na podstawie różnicy ich temperatur wrzenia. Jest to jedna z najstarszych i najczęściej stosowanych metod oczyszczania cieczy, która znajduje zastosowanie w wielu dziedzinach, od przemysłu chemicznego po laboratoria badawcze. Proces ten zazwyczaj rozpoczyna się od podgrzewania mieszaniny, co powoduje odparowanie składników o niższej temperaturze wrzenia. Para następnie przechodzi przez chłodnicę, gdzie skrapla się z powrotem do postaci cieczy. W ten sposób można uzyskać czystszy produkt, eliminując niepożądane substancje. Destylacja może być przeprowadzana w różnych warunkach, takich jak destylacja prosta, frakcyjna czy też próżniowa, w zależności od specyfiki rozpuszczalników oraz wymagań procesu. Kluczowym elementem tego procesu jest odpowiedni dobór sprzętu oraz kontrola parametrów, takich jak temperatura i ciśnienie, co ma istotny wpływ na efektywność separacji.
Jakie są zastosowania destylacji rozpuszczalników w przemyśle
Zastosowania destylacji rozpuszczalników w przemyśle są niezwykle szerokie i różnorodne. W przemyśle chemicznym proces ten jest kluczowy dla produkcji wielu substancji chemicznych, takich jak alkohole, kwasy organiczne czy rozpuszczalniki organiczne. Dzięki destylacji możliwe jest uzyskanie wysokiej czystości produktów końcowych, co jest niezbędne w wielu aplikacjach przemysłowych. Na przykład w przemyśle farmaceutycznym destylacja pozwala na oczyszczanie substancji czynnych oraz usuwanie zanieczyszczeń, co ma kluczowe znaczenie dla jakości leków. Ponadto w branży petrochemicznej destylacja frakcyjna jest wykorzystywana do separacji różnych frakcji ropy naftowej, co umożliwia produkcję paliw oraz innych produktów naftowych. W przemyśle spożywczym destylacja znajduje zastosowanie przy produkcji napojów alkoholowych, gdzie kluczowe jest oddzielenie etanolu od innych składników.
Jakie są różnice między destylacją prostą a frakcyjną
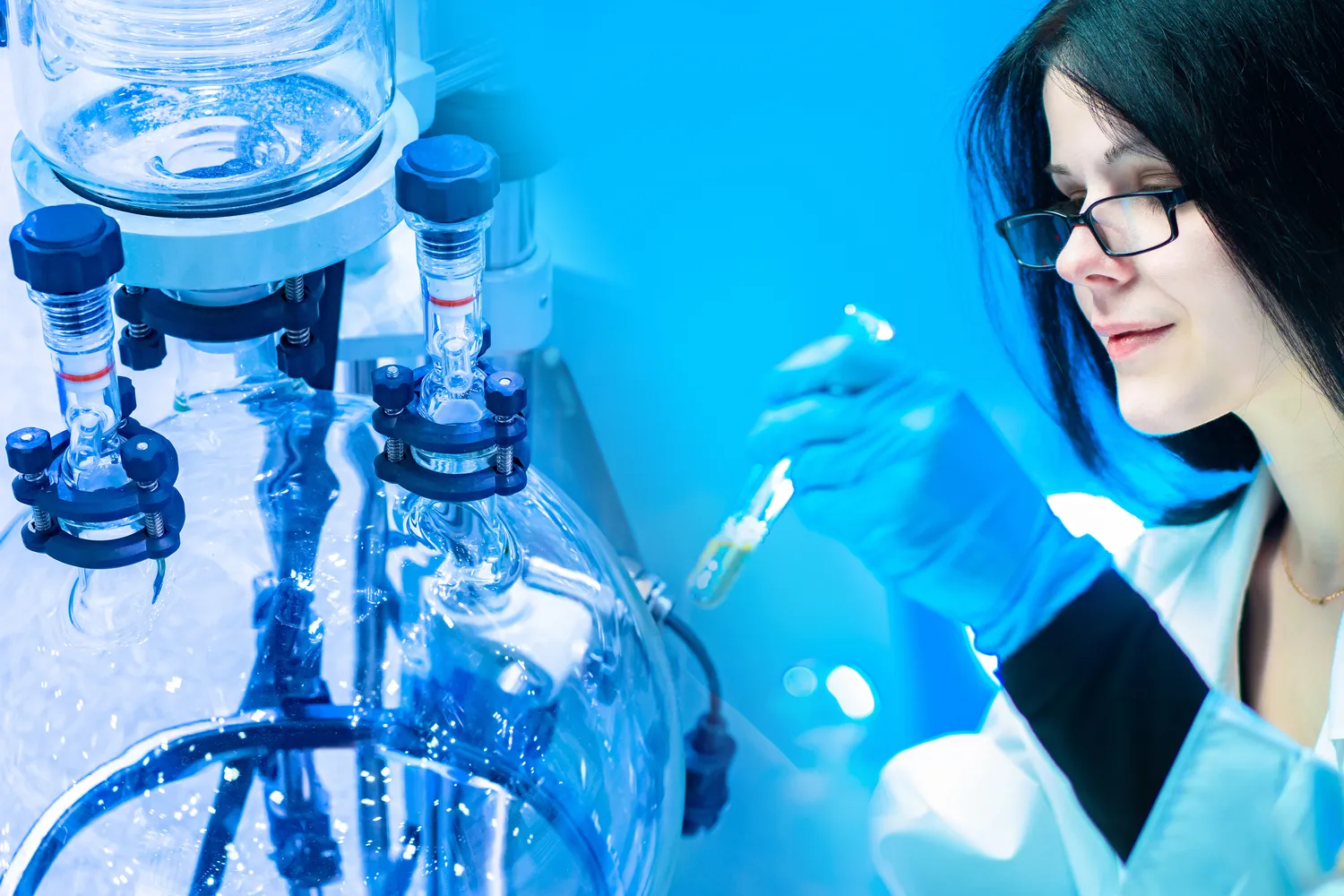
Destylacja prosta i frakcyjna to dwa podstawowe rodzaje procesów destylacyjnych, które różnią się zarówno zasadą działania, jak i zastosowaniem. Destylacja prosta jest stosunkowo prostą metodą, która polega na podgrzewaniu cieczy do momentu jej wrzenia i zbieraniu pary skraplającej się w chłodnicy. Jest ona skuteczna głównie wtedy, gdy różnica temperatur wrzenia składników wynosi co najmniej 25-30 stopni Celsjusza. Z kolei destylacja frakcyjna jest bardziej zaawansowaną techniką, która wykorzystuje kolumny frakcyjne do wielokrotnego skraplania i parowania cieczy. Dzięki temu możliwe jest oddzielanie składników o zbliżonych temperaturach wrzenia, co czyni tę metodę bardziej efektywną w przypadku skomplikowanych mieszanin. Destylacja frakcyjna znajduje zastosowanie w przemyśle petrochemicznym oraz chemicznym do uzyskiwania czystych frakcji różnych substancji.
Jakie są zalety i ograniczenia stosowania destylacji
Destylacja jako metoda separacji ma swoje zalety oraz ograniczenia, które warto uwzględnić przy wyborze odpowiedniej techniki oczyszczania substancji. Do głównych zalet należy możliwość uzyskania wysokiej czystości produktów końcowych oraz szeroki zakres zastosowań w różnych branżach przemysłowych. Proces ten jest również relatywnie prosty do przeprowadzenia i może być skalowany od małych laboratoriów po duże zakłady przemysłowe. Dodatkowo destylacja nie wymaga użycia agresywnych reagentów chemicznych, co czyni ją bezpieczną alternatywą dla innych metod separacji. Niemniej jednak istnieją także pewne ograniczenia związane z tym procesem. Przede wszystkim skuteczność destylacji zależy od różnicy temperatur wrzenia składników; jeśli ta różnica jest niewielka, proces może być mniej efektywny. Ponadto destylacja może być czasochłonna i wymaga odpowiedniego sprzętu oraz kontroli warunków pracy.
Jakie są różnice między destylacją a innymi metodami separacji
Destylacja jest jedną z wielu metod separacji substancji, ale wyróżnia się na tle innych technik, takich jak ekstrakcja, filtracja czy chromatografia. Każda z tych metod ma swoje unikalne cechy oraz zastosowania, co sprawia, że wybór odpowiedniej techniki zależy od specyfiki mieszaniny oraz oczekiwań dotyczących czystości produktu końcowego. W przeciwieństwie do filtracji, która polega na oddzielaniu ciał stałych od cieczy na podstawie wielkości cząsteczek, destylacja opiera się na różnicy temperatur wrzenia. Ekstrakcja z kolei wykorzystuje różnice w rozpuszczalności substancji w różnych rozpuszczalnikach, co może być korzystne w przypadku substancji o niskiej temperaturze wrzenia. Chromatografia to bardziej zaawansowana technika separacji, która pozwala na oddzielanie składników na podstawie ich interakcji z fazą stacjonarną i ruchomą. Choć chromatografia jest często bardziej precyzyjna i skuteczna w separacji złożonych mieszanin, destylacja pozostaje popularnym wyborem ze względu na swoją prostotę i efektywność w przypadku substancji o wyraźnych różnicach w temperaturze wrzenia.
Jakie są najczęstsze błędy popełniane podczas destylacji
Podczas przeprowadzania procesu destylacji można napotkać wiele pułapek i błędów, które mogą wpłynąć na jakość uzyskanego produktu. Jednym z najczęstszych błędów jest niewłaściwe ustawienie temperatury podgrzewania. Zbyt wysoka temperatura może prowadzić do niekontrolowanego wrzenia oraz degradacji termolabilnych składników, co negatywnie wpływa na czystość końcowego produktu. Innym powszechnym problemem jest niewłaściwe dobranie sprzętu destylacyjnego; użycie kolumny frakcyjnej o niewłaściwej długości lub średnicy może skutkować nieskuteczną separacją składników. Należy również zwrócić uwagę na kondensator; jeśli nie jest on odpowiednio chłodzony, para może nie skraplać się prawidłowo, co prowadzi do strat materiałowych. Kolejnym błędem jest niedostateczna kontrola ciśnienia atmosferycznego; w przypadku destylacji próżniowej niewłaściwe ustawienia mogą prowadzić do nieefektywnego procesu. Ostatnim istotnym aspektem jest brak odpowiedniego monitorowania jakości uzyskiwanych frakcji; regularne pobieranie próbek i ich analiza pozwala na bieżąco oceniać efektywność procesu i wprowadzać ewentualne korekty.
Jakie są nowoczesne technologie związane z destylacją
Nowoczesne technologie związane z destylacją ewoluują wraz z postępem naukowym i technologicznym, co wpływa na efektywność oraz jakość procesów separacyjnych. Jednym z przykładów są systemy destylacji próżniowej, które umożliwiają przeprowadzanie procesów w obniżonym ciśnieniu, co pozwala na destylację substancji o wysokiej temperaturze wrzenia bez ryzyka ich degradacji. Tego typu technologie znajdują zastosowanie głównie w przemyśle farmaceutycznym oraz chemicznym, gdzie czystość produktów jest kluczowa. Innowacyjne podejścia obejmują także zastosowanie nanotechnologii w konstrukcji kolumn frakcyjnych, co zwiększa powierzchnię kontaktu między parą a cieczą, a tym samym poprawia efektywność separacji. Dodatkowo rozwijają się technologie automatyzacji procesów destylacyjnych, które pozwalają na precyzyjne monitorowanie parametrów pracy oraz automatyczne dostosowywanie warunków do zmieniających się potrzeb produkcyjnych. Warto również wspomnieć o zastosowaniu sztucznej inteligencji w optymalizacji procesów destylacyjnych; algorytmy AI mogą analizować dane operacyjne i sugerować zmiany w czasie rzeczywistym, co prowadzi do zwiększenia wydajności i redukcji kosztów produkcji.
Jakie są przyszłe kierunki badań nad destylacją rozpuszczalników
Przyszłe kierunki badań nad destylacją rozpuszczalników koncentrują się na poszukiwaniu bardziej efektywnych i ekologicznych metod separacji substancji chemicznych. W obliczu rosnącej potrzeby ograniczenia zużycia energii oraz minimalizacji odpadów, naukowcy badają nowe materiały do budowy kolumn frakcyjnych oraz kondensatorów, które mogłyby poprawić wydajność energetyczną procesów destylacyjnych. Ponadto rozwijają się badania nad wykorzystaniem biotechnologii w procesach oczyszczania; enzymy i mikroorganizmy mogą być stosowane jako alternatywne metody separacji substancji chemicznych, co może przyczynić się do zmniejszenia negatywnego wpływu na środowisko. Kolejnym interesującym kierunkiem jest integracja procesów destylacyjnych z innymi technologiami separacyjnymi, takimi jak ekstrakcja czy adsorpcja; takie podejście może prowadzić do uzyskania lepszej jakości produktów oraz większej efektywności całego procesu. Również rozwój technologii cyfrowych i sztucznej inteligencji otwiera nowe możliwości dla optymalizacji procesów przemysłowych; modele predykcyjne mogą pomóc w lepszym zarządzaniu parametrami pracy urządzeń destylacyjnych.
Jakie są kluczowe czynniki wpływające na efektywność destylacji
Efektywność procesu destylacji jest uzależniona od wielu czynników, które należy wziąć pod uwagę podczas projektowania i przeprowadzania tego typu operacji. Jednym z najważniejszych aspektów jest różnica temperatur wrzenia składników mieszaniny; im większa ta różnica, tym łatwiejsze i bardziej efektywne będzie oddzielenie substancji. Kolejnym kluczowym czynnikiem jest ciśnienie, które wpływa na temperaturę wrzenia; obniżenie ciśnienia może umożliwić destylację substancji o wysokiej temperaturze wrzenia w niższej temperaturze, co minimalizuje ryzyko ich degradacji. Warto również zwrócić uwagę na konstrukcję kolumny frakcyjnej; jej długość, średnica oraz liczba teoretycznych tac mają znaczący wpływ na efektywność separacji. Dodatkowo prędkość przepływu pary oraz cieczy w kolumnie powinny być odpowiednio dostosowane, aby zapewnić optymalne warunki kontaktu między fazami. Ostatnim istotnym czynnikiem jest jakość używanych materiałów; zanieczyszczenia mogą wpływać na wyniki destylacji, dlatego ważne jest stosowanie wysokiej jakości reagentów oraz czystych rozpuszczalników.